7 Common EIFS Problems
EIFS (Exterior Insulation and Finish Systems) can fail due to improper installation, physical damage, or moisture issues. Understanding these common problems prevents costly repairs and extends the lifespan of your EIFS-clad building.
In this guide, we’ll cover the 7 most common EIFS failures and how to prevent them.
Jump right in:
- Improper Installation Leads to Moisture Retention – Ensuring proper sealing and a drainage system is key.
- Holes, Dents, or Scrapes from Impact Cause Water Infiltration – Reinforced mesh and protective barriers help prevent damage.
- Cracks Form Due to Temperature Changes – Expansion joints and flexible materials absorb movement.
- EIFS Peeling Away from the Wall – A strong bond and correct installation prevent detachment.
- Mold Growth from Trapped Moisture – Good ventilation and waterproofing keep mold away.
- Staining and Discolouration – Using quality finishes and regular maintenance stops unsightly stains.
- Insect Infestation – Sealing gaps and using treated materials prevent pests.
Each of these failures can cause severe damage if left unaddressed. Keep reading to learn how to protect your EIFS system with expert solutions!
If you have additional questions or need EIFS services in Edmonton, AB, call (780) 710-3972.
1. Improper Installation Leads to Moisture Retention
Prevention: Get Our Professional Installation that Ensures Sealing and Drainage System Install
EIFS keeps water out, but improper installation can lead to moisture getting trapped behind the system. This causes mould, rotting wood, and other severe damage.
Why This Happens:
- Gaps in sealants around windows and doors allow water to get behind the EIFS.
- A missing or poorly installed drainage layer prevents water from escaping.
- Incorrect flashing around rooflines, balconies, or wall joints directs water into the EIFS instead of away.
How We Prevent It:
- We apply high-quality sealants around windows, doors, and joints, checking them annually for wear.
- We install a drainage EIFS system, which includes a moisture barrier behind the foam insulation.
- We use proper flashing techniques to ensure water flows away from the building.
- We test for water infiltration after installation to catch issues early.
Get Professional EIFS Installation
Depend Exteriors offers professional EIFS installation to prevent moisture retention, ensuring your home or business stays protected from water damage, mould, and structural issues. Our expert EIFS contractors serve Edmonton and Alberta, delivering durable, energy-efficient, and aesthetically pleasing exterior solutions.
Why Choose Depend Exteriors?
✔ 15+ Years of Experience – Trusted stucco experts in Alberta.
✔ Licensed & Bonded – Fully insured for your peace of mind.
✔ High-Quality Workmanship – Precision and durability in every project.
✔ EIFS Specialists – Prevent moisture issues with expert installation.
✔ 100% Customer Satisfaction – Proven track record with happy clients.
📞 Call (780) 710-3972 for a free estimate!
2. Holes, Dents, or Scrapes from Impact Cause Water Infiltration
Prevention: Install Protective Barriers and Reinforced Mesh
EIFS can get damaged by everyday activities, like moving furniture, using ladders, or exposure to hail. When the outer layer is punctured or scraped, water can seep into the insulation beneath. Once moisture gets trapped, it can lead to mould growth and structural damage.
Why This Happens:
- EIFS has a soft, foam-based layer under the finish that is easily damaged by force.
- Areas near the ground, doorways, and corners are more likely to experience impact damage.
- Even small punctures can let in moisture without repairs, leading to hidden issues over time.
How to Prevent It:
- Apply impact-resistant mesh in areas prone to damage, such as lower walls and near doorways.
- Install protective barriers, like bollards or kick plates, in high-traffic areas.
- Train maintenance staff and residents to avoid leaning ladders or dragging equipment against EIFS walls.
- Inspect regularly and repair any cracks or dents before they worsen.
3. Cracks Form Due to Temperature Changes
Prevention: Use Expansion Joints and Flexible Materials
Buildings naturally expand and contract as temperatures change. If EIFS cannot flex with these movements, cracks form in the finish. These cracks allow water to get inside, leading to hidden damage over time.
Why This Happens:
- Large walls without expansion joints can’t absorb movement, leading to cracks.
- Temperature swings cause EIFS to contract and expand, stressing the material.
- Low-quality or rigid adhesives and coatings cannot handle the stress of movement.
How to Prevent It:
- Install expansion joints in large wall sections to allow controlled movement.
- Use flexible, high-quality adhesives that can withstand temperature changes.
- Inspect EIFS walls regularly for small cracks and repair them immediately before they expand.
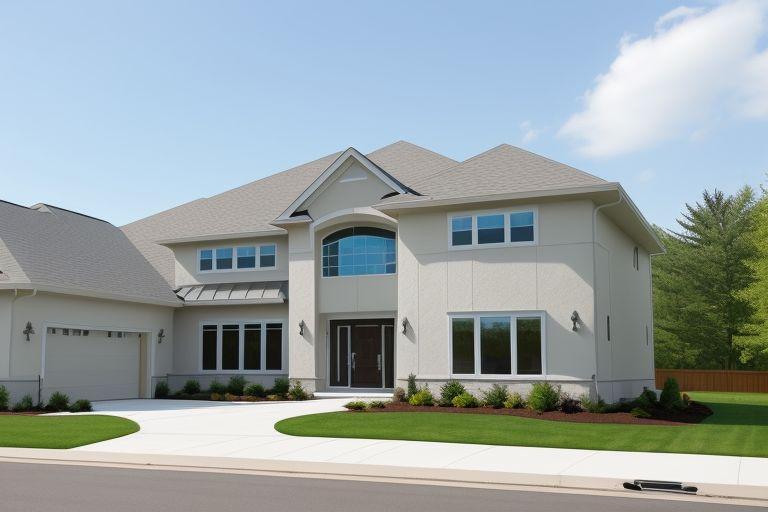
4. EIFS Peel Away from the Wall
Prevention: Ensure a Strong Bond with Our Proper Installation
EIFS must be securely attached to the building. If the layers separate from the wall, water can enter behind the system, leading to serious structural issues.
Why This Happens:
- Not enough adhesives or fasteners were used during installation.
- The surface underneath EIFS was dirty or damp, preventing a strong bond.
- Water intrusion behind the EIFS weakened the attachment over time.
How to Prevent It:
- Ensure the surface is clean and dry before applying EIFS.
- Use the recommended amount of adhesive and follow the manufacturer’s instructions.
- Allow for proper curing time before applying the final finish.
- Include a moisture-resistant barrier behind the EIFS to protect against water damage.
5. Mold Growth from Trapped Moisture
Prevention: Improve Ventilation and Waterproofing
If moisture gets trapped behind EIFS, it creates the perfect environment for mould and mildew. This damages the building and causes health problems for occupants.
Why This Happens:
- Poor drainage allows water to sit behind the EIFS instead of escaping.
- Sealants break down over time, allowing moisture to enter.
- High humidity levels make it easier for mould to grow inside the walls.
How to Prevent It:
- Use a drainage EIFS system that lets moisture escape before it causes damage.
- Choose mould-resistant insulation materials inside EIFS walls.
- Inspect and replace worn-out sealants before they start allowing water in.
- Maintain proper ventilation inside and outside the building to reduce humidity buildup.
6. Staining and Discolouration
Prevention: Use Quality Finishes and Proper Maintenance
EIFS walls can develop stains over time due to water intrusion, dirt buildup, or biological growth, such as algae.
Why This Happens:
- Water seeps into the EIFS and carries contaminants that leave stains.
- Airborne pollutants settle on the surface and mix with moisture.
- Algae and mould grow on damp surfaces exposed to humidity.
How to Prevent It:
- Apply water-resistant coatings to repel moisture and stains.
- Clean EIFS surfaces regularly to prevent dirt buildup.
- Trim trees and bushes away from walls to improve airflow and reduce moisture retention.
7. Insect Infestation
Prevention: Seal Gaps and Use Treated Materials
Certain insects, such as termites and ants, can tunnel into EIFS, causing structural damage and allowing moisture to enter.
Why This Happens:
- Small gaps or cracks in EIFS allow insects to enter.
- EIFS provides a warm, sheltered space for insects to nest.
- Moist conditions attract insects looking for food sources.
How to Prevent It:
- Seal all gaps and cracks with high-quality sealant to prevent insect entry.
- Treat EIFS with insect-resistant coatings if needed.
- Keep EIFS dry to reduce the likelihood of insect infestations.
EIFS Failures and Their Solutions (Common Repair Mistakes and How to Fix Them)
Repairing EIFS (Exterior Insulation and Finish Systems) requires precision and expertise. Mistakes during the repair process can lead to moisture issues, structural damage, and a shortened system lifespan.
Below are common EIFS repair mistakes and how to fix them properly.
1. Improper Patching of Damaged Areas
Failure: Using the wrong materials or techniques when patching damaged EIFS can result in weak spots, allowing moisture to enter. Some contractors use non-EIFS patching materials, which do not properly bond or expand and contract with the system.
Solution:
✔ Use EIFS-compatible patching compounds that bond seamlessly with the original system.
✔ Feather the edges of the patch to blend with the existing surface.
✔ Match the texture and colour of the surrounding area for a uniform finish.
2. Inadequate Sealing Around Windows and Doors
Failure: Failing to properly seal EIFS around windows, doors, and other penetrations allows water to seep behind the system, leading to mould and deterioration. Many repair jobs overlook resealing after patching.
Solution:
✔ Apply high-quality, flexible sealants around all openings.
✔ Inspect and replace old, cracked, or missing caulking regularly.
✔ Ensure all penetrations are flashed correctly to direct water away.
3. Skipping the Drainage System During Repairs
Failure: Older EIFS systems did not include a drainage layer. Some contractors fail to integrate modern moisture management solutions when repairing these systems, leading to water buildup behind the surface.
Solution:
✔ Upgrade to a drainage EIFS system that allows moisture to escape.
✔ Install weep screeds at the base of walls to help drain excess water.
✔ Ensure a proper water-resistant barrier is applied behind EIFS during major repairs.
4. Using the Wrong Mesh or Insufficient Reinforcement
Failure: Not using proper reinforcing mesh or applying it incorrectly can cause cracking and impact damage, reducing the system’s durability.
Solution:
✔ Use high-impact EIFS mesh in vulnerable areas, such as lower walls and corners.
✔ Ensure mesh is fully embedded in the base coat to prevent delamination.
✔ Overlap mesh properly at seams to maintain strength.
5. Ignoring Cracks Instead of Repairing Them Correctly
Failure: Simply filling in cracks with paint or caulk instead of addressing the underlying cause results in repeated cracking and moisture penetration.
Solution:
✔ Identify the cause of cracking (thermal movement, impact, or substrate issues).
✔ Use flexible EIFS-compatible patching materials instead of just paint or caulk.
✔ Add control joints if cracking is due to structural movement.
6. Painting Over EIFS with the Wrong Type of Paint
Failure: Using non-breathable paints traps moisture inside the system, leading to bubbling, peeling, and damage over time.
Solution:
✔ Use EIFS-approved breathable coatings that allow moisture to escape.
✔ Avoid oil-based or waterproof paints that can seal in moisture.
✔ Ensure the EIFS surface is clean and dry before painting.
7. Not Matching the Texture and Finish During Repairs
Failure: Poor blending of repaired areas creates visible patches and inconsistencies, affecting curb appeal.
Solution:
✔ Use the same finish coat material and texture as the original EIFS.
✔ Feather the repair edges for a smooth transition.
✔ If the repair area is large, consider recoating the entire wall for a uniform look.
8. Failing to Address Moisture Damage Before Repairs
Failure: Covering up damaged EIFS without addressing underlying moisture problems leads to hidden rot and future failures.
Solution:
✔ Inspect for trapped moisture using infrared scans or moisture meters.
✔ Remove and replace water-damaged substrate or insulation before applying new EIFS.
✔ Install proper drainage and flashing to prevent future moisture buildup.
9. Applying EIFS Over an Unprepared Surface
Failure: Trying to repair EIFS over a dirty, damp, or unstable surface weakens adhesion and leads to peeling or separation.
Solution:
✔ Clean and dry the repair area before application.
✔ Use primer or bonding agents if required.
✔ Ensure the substrate is stable and free from loose materials before reapplying EIFS.
10. Attempting DIY Repairs Instead of Hiring Professionals
Failure: EIFS repairs require specialized materials and techniques. Many DIY attempts fail due to improper materials, inadequate sealing, or poor blending.
Solution:
✔ Hire experienced EIFS professionals who understand the system’s requirements.
✔ Get a thorough inspection before repairs to identify all issues.
✔ Ensure the repair follows manufacturer guidelines for long-lasting results.
FAQs About EIFS
What are the most common areas where failures develop in EIFS?
The most common areas where EIFS failures develop are around windows, doors, rooflines, and wall penetrations. These areas are vulnerable due to improper sealing, lack of flashing, and exposure to moisture. Other high-risk locations include ground-level sections where impact damage can occur and large uninterrupted wall sections that lack expansion joints.
What causes EIFS to crack?
EIFS cracks develop due to thermal expansion and contraction, improper installation, and building movement. If the system lacks proper expansion joints, stress from temperature changes can lead to cracks. Insufficient substrate preparation, low-quality adhesives, and moisture infiltration can weaken the EIFS, making it more prone to cracking.
What is the life expectancy of EIFS?
The life expectancy of EIFS is between 30 to 60 years with proper installation and maintenance. The longevity depends on factors such as weather exposure, maintenance routine, and quality of installation. Regular inspections and timely repairs can extend the lifespan and prevent costly failures.
What is the main problem with EIFS products?
The primary issue with EIFS is moisture retention, especially when installed without a proper drainage system. If water gets trapped behind the system due to poor sealing, missing flashing, or impact damage, it can lead to mould growth, wood rot, and structural deterioration. Proper installation with a drainage system, high-quality sealants, and regular inspections can mitigate this issue.
How often do you need control joints in EIFS?
Control joints should be placed in EIFS every 10 to 25 feet, depending on the wall size and structure. They are necessary at every floor line, where material changes, and when EIFS meets dissimilar surfaces. Properly placed control joints help absorb building movement and prevent cracking and system failure.
What is the Problem with EIFS Cladding?
The main problem with EIFS cladding is moisture retention, leading to mould growth, wood rot, and structural damage if water gets trapped behind the system. Unlike traditional stucco, EIFS does not naturally allow moisture to escape, making proper installation and maintenance crucial to prevent failures.